In this article you will understand the importance of using the hotend X to print fiber-filled materials.
The hotend X - 0.6 mm is only compatible with the BCN3D Epsilon 3D printer and is the correct hotend to print BCN3D fiber-filled materials PP GF30 and PAHT CF15.
Below you can see some amazing photos provided by E3D lab that show the negative effects nozzles can have when coming into contact with with materials like PAHT-CF15 and PP GF30.
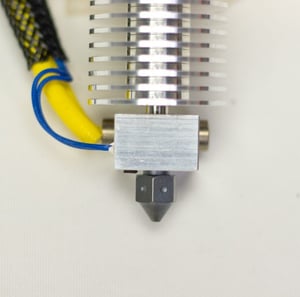
But let's start from the beginning to fully understand the issue.
The standard hotends use brass nozzles. These were designed to be used with soft filaments like PLA, ABS, PP, etc. But nowadays the 3D printing industry demands other materials with new properties. Which brings us to fiber filled materials.
The downside? These materials are much more abrasive, they literally act like metal files when are extruded thought the nozzle. As you will see, it is not necessary to print many meters of these filaments to start causing irreparable damage to your brass hotends.
These painful pictures were taken after printing just 250gr of carbon fiber filled filament, using a brand new brass 0.4mm nozzle. You can compare the wear of the hotend X after printing 2.5 kg of various carbon filled materials, and glass filled materials too "right side hotend". Ten times the amount of material (250g) that the brass nozzle on the left has printed.
The pictures are self-explanatory, the tip of the brass nozzle has worn down making the nozzle shorter in overall length, causing, for sure, calibration issues. The tip of the nozzle has also been rounded over into a dome shape due to abrasion.
The nozzle orifice has been opened up in diameter making it bigger than 0.4mm. The wear is greatest in the middle, it hasn't been uniformly worn, causing an ovoid type wear cavity in the nozzle orifice.
BCN3D printing configurations will be not longer compatible with this "impossible to determine diameter" brass nozzle.
The difference between the soft inner surface on the X hotend and the surface striation on the brass nozzle is clearly visible. These irregularities on the internal wall cause greater friction, making it difficult to extrude the material, the under extrusion issue is knocking the door.
The hardened X nozzle has completely retained its original shape with zero observable wear.
The solution! Let's see now how the hotend X has been designed to prevent that issue.
Fortunately E3D team has "just as they say" sacrificed some nozzles at the altar of carbon and glass fiber filaments. They did enough tests in order to produce a harder nozzle.
E3D has carefully selected the steel to produce the hotend X and has included a combination of thermal and chemical treatments on the post-processing, creating an extremely hard and wear resistant nozzle.
To further increase the hardness and smoothness the nozzle X is plated with slick nickel. Then, the entire nozzle receives a ‘polyphobic’ nano-coating which prevents polymer adhering to the nozzle surface.
- Less build up, particularly of sticky and filled materials to the nozzle cone.
- Improved first layer reliability; the slick coating has a reduced tendency to ‘drag’ material, particularly at sharp corners where tracks can peel up.
- Slicker, smooth top solid layers with a glassy like finish as a result of the smooth laydown of material.
- Easier nozzle cleaning, what little material that does adhere is easily wiped away with a paper towel leaving a very clean nozzle.
It's possible to get the same benefits using jewel tip nozzles, but this kind of nozzles restricts the flow due to an internal ‘step’ in the polymer flow path. This causes poor flow response, high back-pressure, and starvation of extrusion.
Hotend X tips are machined in one single piece providing a fantastic flow response and keeps exactly the same geometry and compatibility as the rest of the BCN3D hotends.
You can help improve the BCN3D Knowledge Base. If you feel there are guides that we are missing or you found any error, please use this form to report it. Report form :) |